Taking a hand-drawn design and transforming it into a 3D sculpture needed to make coins is, to say the least, fascinating to watch. Artists at the United States Mint in Philadelphia do it nearly every day.
Just this past Tuesday, Cassie McFarland’s design depicting a baseball glove created news headlines since it will appear on obverses (heads side) of next year’s National Baseball Hall of Fame Commemorative Coins. In behind-the-scene news, U.S. Mint Sculptor-Engraver Don Everhart embraced the responsibility of interpreting her design to sculpt it in clay and create it in plaster.
Numismatists will recognize Don, having designed and sculpted many of America’s exceptional medals and coins.
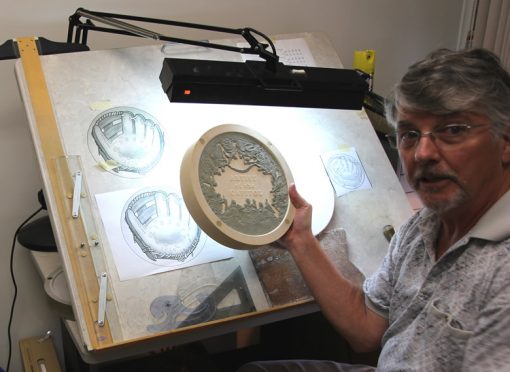
In a recent trip to the Philadelphia Mint, we watched Don perform magic in sculpting fine details on his plaster model of McFarland’s baseball glove design. It was a surreal moment as he talked, showed us examples of his work and put tool to plaster to enhance this unique, curved-shape design. We thank him for the experience.
Today, we offer a brief photo walkthrough of Don in action. We also add some background on how McFarland’s design went from paper to plaster and will eventually get pressed on $5 gold, silver dollar and clad half-dollar Baseball commemorative coins.
To kick things off, here is a short video of Don making refinements on his plaster model of the baseball glove design. We slowed the video down a bit so you can get a better look.
Before getting to the plaster model, Don had to take McFarland’s hand-drawn design and sculpt it into clay.
The photo of Don with the 3D clay model is demonstrative. It was created from a flat line art design, as had to be done for the baseball glove design. Here’s a closer view of that sculpted clay model as it gives a better sense of it all.
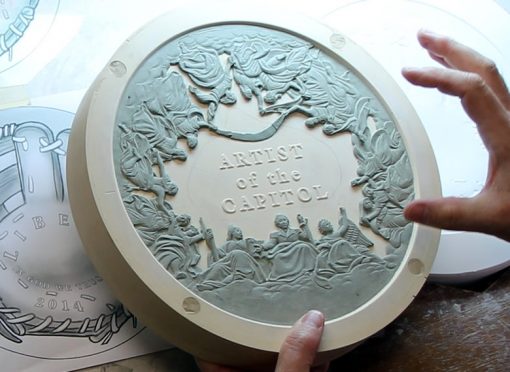
Once the clay model is completed, it is captured to plaster where finer details may be shaped. It was this sculpting stage of the baseball glove design that Don was working on when we stopped by.
Sculptors have an array of small tools for working in clay and plaster. Here is one of the tools Don used on the plaster model to sketch subtle details.
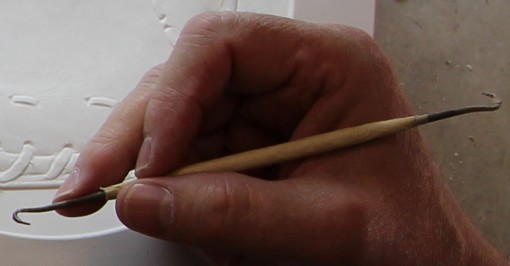
Visual tools are often used in designing and sculpting as well. Cassie McFarland was inspired by a glove used by her family while she was growing up. She used it to guide her design. Don relied on Cassie’s drawing for his sculpting in both clay and plaster, but also on his son’s baseball glove.
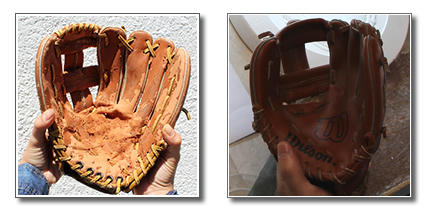
Here, Don holds his son’s glove and Cassie’s original baseball glove design, describing how he uses them both as he sculpts.
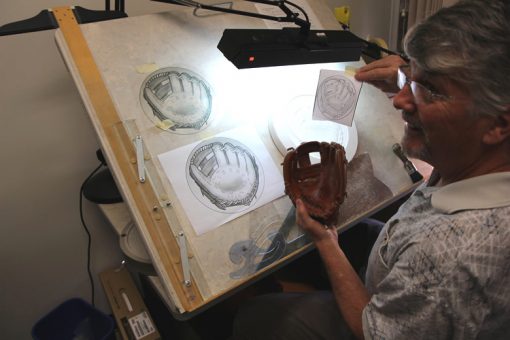
In Cassie’s design, she placed wheat sheaves on the glove. In her narrative submitted with it, she noted that the:
"Two wheat sheaves unite with the braided lace of the glove to form a ring. This stands for American unity, stitched together to form one nation. The wheat celebrates a love for our bountiful land and home."
Here’s a closer look at her design with sheaves on the glove.
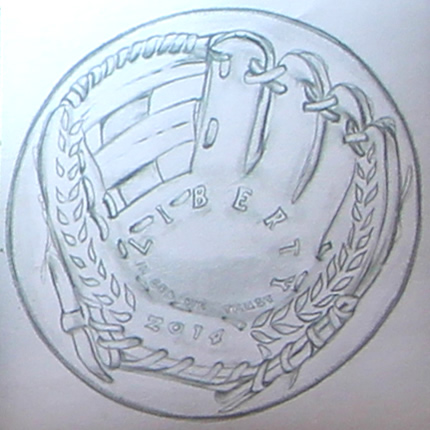
Members of the Commission of Fine Arts (CFA) and National Baseball Hall of Fame preferred her design without the two wheat sheaves, and they were subsequently removed. That meant a revised line art design without them had to be created.
In this photo of Don, notice his working area toward the left has two line art designs without the sheaves.
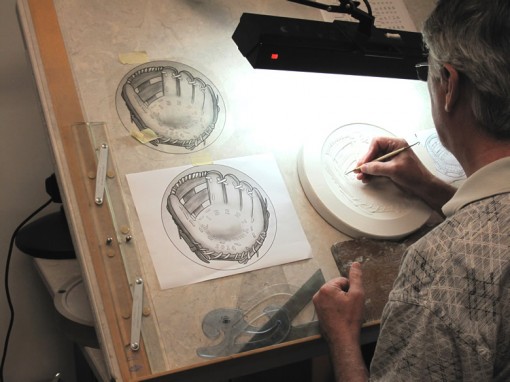
Here, one more photo of Don sculpting in plaster. This view from the right side shows Cassie’s original design taped to his working area, also being used as a guide.
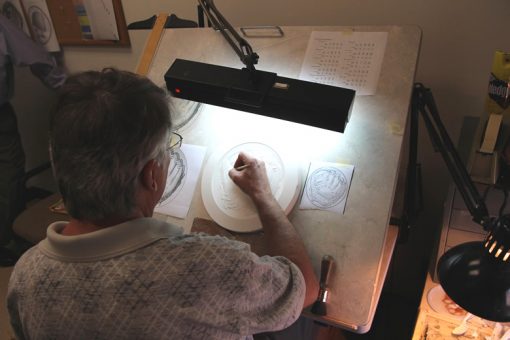
Finally, a close-up photo of Don’s plaster model. Notice that it still lacks the inscriptions of "LIBERTY," "IN GOD WE TRUST," "2014," and the initials of Cassie and Don.
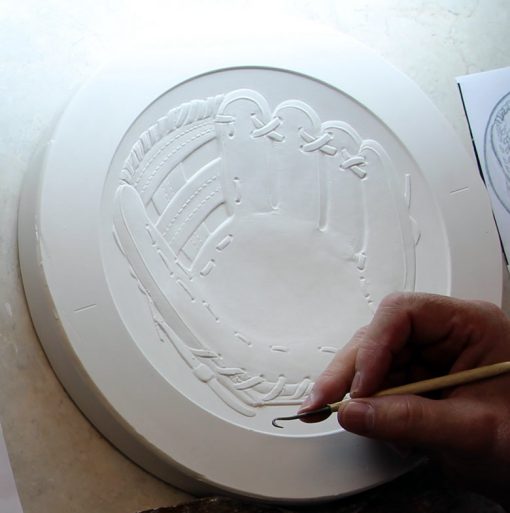
Don uses the traditional method of sculpting in clay and plaster whereas some Mint artists rely on computer software to sculpt digitally, like Joe Menna, or a mixing of both like Phebe Hemphill.
Read: US Mint Artists at Philadelphia Sculpt Digitally and in Clay.
After plaster models are completed, a high resolution scanner is used to map their details digitally. This digital information is then sent to digital design software for further tweaks, if needed.

With the sculpt digitally captured, master hubs and dies are cut from steel blanks using a Mikron CNC milling machine.

Working dies bear the negative image of a coin’s design. When completed, an obverse and reverse die are fitted inside a high-tonnage press. A metal disc called a blank is placed between the two dies, pressure is applied and the coin is created. This description of the minting process is extremely abbreviated. If you’re interested in much more information, learn about hubs and dies or check out our series of articles for the step-by-steps on the coin production process at the Philadelphia Mint.
In the end, here is a rendering of what Cassie’s obverse design will look like on next year’s 2014 $1 National Baseball Hall of Fame Silver Commemorative Coin. (The same design will appear on $5 gold Baseball commemorative coins and 50c clad Baseball commemorative coins.)

Cassie has the credit for her design and Don for sculpting it. Don has also earned credits for both designing and sculpting reverses for the 2014 Baseball Commemorative Coins.

That’s it for this article. Thanks for stopping by CoinNews.net.
will the mint show us a step by step on how they make unc. silver eagles with mint mark and how they do the finish on them. thanks